A penge megmunkálás
Rátérve a feldolgozott külső és belső hengeres, kúpos, gömb alakú, forgásfelület alakú testek, valamint azok lapos végét felületeken.
A műveletek száma és átmenetek, azok sorrendjét határozza meg mérete és minősége a munkadarab. Az átlagolt adatokat minőségű feldolgozó részek során esztergálás, eszterga kapott táblázatban mutatjuk be. 1. Eljárás fordulva végrehajtani termelés eszterga, amely attól függően, hogy milyen típusú termelési egyetemes lehet szerelve CNC rendszerek vagy merev cam ellenőrzés.
Nagyobb teljesítmény érhető el mind eszterga telepíteni több eszközt (tornyokkal vagy féknyergek) működő, egymás után vagy párhuzamosan, és nagyobb számú orsó a gép, amely lehetővé teszi, hogy egyszerre feldolgozni különböző felületeinek az alkatrészeket.
Megmunkáló központok, felszerelt kiegészítő orsó termelnek marás, fúrás és a különböző oldali homlokfelületek. Rögzítése a munkadarabot a gép olyan eszközökkei, amelyek hozhat létre vagy aszimmetrikus konszolidációs erőfeszítések, vagy axiálisan szimmetrikus.
Az első (állkapocs tokmány, hüvely, tüskék cam) nagyon konszolidációs erőfeszítés és úgy tervezték, nagyoló és simító műveletet. Befejező műveleteket végeznek, ha a rögzítő tengelyszimmetrikus alkatrészek ami növeli vibráció ellenállás és minősége.
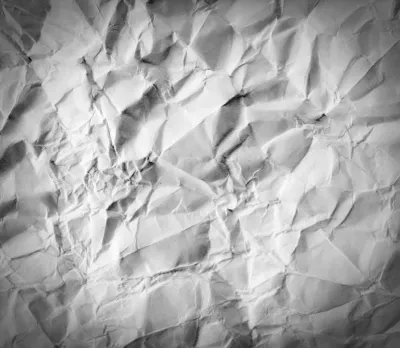
A külső részek felületein, amelynek hossza nagyobb, mint 6-szor az átmérő, szerelt esztergacsúcsok. Center furatok készült részletesen háromféle típusától függően tételek, és a görgők átmérője kisebb, mint 4 mm ajánlott külső pivot kúp.
Hollow egységeire (hengerek, hüvelyek) fel van szerelve a eszterga merev tüskék (kúpos, hengeres, és bemetszett) vagy expander (Collet, görgős, és egy vékony falú pruzhinchatyh deformált fal).
A kezelés nem merev alkatrész, amelynek hossza nagyobb, mint az átmérője 12-szer vagy több, több oporylyunety használt, amely együtt mozog a kocsi vagy felszerelhető rögzítetten a gépállványhoz. A fő típusa szerszám, amellyel köszörült rész a metszőfogak, amely az ilyen típusú műveletek vannak osztva folyamatos, unalmas, vágás és karcolás.
Persely vágó használják köszörülés külső felületei forgástestek és vannak osztva egyenes és hajlított. Bent jobb és bal kommunikáló metszőfogak gyakoribbak miatt megnövekedett merevséget és a lehetőséget, nem csak a fordulópont ólom felületén, hanem a néző és a letörés.
, Átmenő vágó a tervezési gyártják keményforrasztással lemezeket GOST 18877 szög szempontjából F = 45 °, GOST 18878 szög szempontjából p egyenlő 45, 60 és 75 ° (az utolsó végrehajtott F1 egyenlő 15 és 25 °), GOST 18879 - vágó, a folyamatos tolóerő egyenes és íves f = 90 °.
Széles körben használt eszterga szerszám mechanikai rögzítéssel váltólapkákkal. GOST 26.476 azonosított négy fő áramkörök rögzítésére váltólapkákkal szánt különböző típusú szerszámtartó, és GOST 26.613 meghatározza az alapvető követelményeket vágó mechanikai rögzítéssel ezeket a lemezeket.
A leginkább megbízható rögzítését a lemezek biztosítja rögzítését egy ék-markolat, amely szintén előfeszíti a lemez és a csap, a központosító tárcsa és annak támasztófelületet.
Az ilyen vágó állnak három típusú lemez: háromszögletű f = 92 °, a tetraéderes F = 45 ° és a hatszög df = 45 °. Kontúr és alakú élesítés alkalmazott parallelogramma lemez, amelynek méreteit határozzák meg GOST 20872.
Unalmas eszközök működnek összetettebb környezetben, mint a kommunikáció miatt csökkent merevséget és összetettsége chip. A megmunkálás lyukak átmérője 8 mm használunk 3. Tömör vágó készült karbid acél szár, átmenő furatokhoz - GOST 18062 és süket - GOST 18063. Ezek a vágó van akár négyzetes vagy hengeres szárral és rendelkezésre állnak a három típusa számára koordinatnorastochnyh gépek, automatikus eszterga és esztergagépek.
Bizonyos esetekben, kétoldalas penge, és alkalmazza éli unalmas fej, amely jobb teljesítményt, de kevésbé rugalmas.
A nagy szigorúságú unalmas vágó, fokozott rezgésállóságot és sima chip mentesítés aránya az átmérője a vágó és a tüske furata 0,8-0,5, és az átmérője a vágó és a tüske tartományok 0,3-0,2.
Széles körben elfogadott unalmas vágó a mechanikailag rögzített betétkést: háromszög alakú f = 90 °, szögletes lemezekre, ahol p értéke 75 és 45 °, és a rombusz alakú lemezek df = 95 ° (GOST 26.612).
Elővágó tervezték csiszolására síkokban merőlegesek a forgástengelyre és szemben naprohod keresztül előtolás. Elővágókhoz is kapható forrasztott lemezek (GOST 18893) az íves típusú nagy dinamikus terhelések és közvetlen típusát. Pontozás vágó mechanikai rögzítéssel lemezeken előállított háromszög alakúak, f = 90 °, és a hajlított - pozitív és negatív homlokszög, és a lemezeket egy négyzet alakú df = 75 °.
Vágópenge használják vágás darab és alkatrészek eszterga. Ezek a vágó működnek egy fej, amelynek szélessége kisebb, mint a szélessége a szerszám testhez, de dolgozott formában nagyobb merevséget.
A fej hossza alapján választjuk példány meghatározott átmérőjű, de általában nem több, mint 130 150 mm. GOST 18884 vágópengék négyféle változatban. Az első végrehajtási lemez, amelynek ferde felületeket, forrasztott ferde horony a tartó, ami növeli a felülete a felfekvő, hogy a tulajdonos, a közös szilárdság, kisebb töredezéseinek és a lemez.
A második lemez egy sík felületre kapcsolatok teszik őket feldolgozható, de csökkenti a dinamikai erejét. A harmadik és negyedik végrehajtása különböznek jelenléte által a fenti húzott feje ízjavító erőt metszőfogak. Ez úgy érhető el a segítségével élezés vágó bizonyos kis szögben terve és hátsó sarkát a kisegítő vágási éleket, amely magas minőségű csiszolás és pontos telepítést a gépen.
Ahhoz, hogy teljes feldolgozásának egyik végén a részek, mint a szegmens nélkül, központi rúd fő vágóéi éles szögben 90 °, és az f = 75. 80 °.
Annak érdekében, hogy megkönnyítsék a beszúró vágás vágó, eltűnő feltételek chipek és történő kivonásának lehetőségét, a vágóéi éles-szimmetrikusan sarkokkal szempontjából F = 60. 80 °, vagy két letörésekkel szimmetrikus mindkét oldalán egy méret b = 1,0-1,5 mm szögben 45 °.
CNC eszterga és robot rendszerek kellett változtatni a design vágó.
Elterjedt kap egy blokk vágó design. ahol a vágólap van beszerelve a vágó bölcső telepítve a tulajdonos. Incisal zárolástartó egy bonyolult konfiguráció erősítésüket szerszámtartó, amely lehetővé teszi a gyors váltást az automatikus és pontos rögzítésére a gép mind radiális irányban, és a magassága.
Ezek a rugalmas támaszok V-alakú vájatok egy szög 90 °, amely lehetővé teszi, hogy hatékonyan alkalmazzák autooperator cseréje betétek.
Szerelőcsavar mechanizmust vezetnek, amelyek kisméretű elmozdulások - csak egy vagy másfél fordulatot, és a kis nyomatékot.
A főbb típusai a rögzítőlap egy lyuk - csavar, ék-tack és a lengőkar. Csavar talált legnagyobb felhasználásra befejezni esztergálás és unalmas, jó forgácseltávolítás és jó hozzáférést biztosít a kezelési felület; Nem ajánlott nagyoló.
Alkalmazása egy ék ragasztás némileg bonyolítja a szerelési szerkezet, de hatékonyabban nagyolás közben.
Rocker kar biztosítja a leghatékonyabb lámpatest nagyoló, biztosítva a jó forgácseltávolítás, gyors változás sokféle lemezek.
A lemezeket szerelt megnyitása nélkül markolat, hogy használják a befejező.
Amikor fordul használják több mint 60 fajta betétkések különböző geometriai alakzatokat. Válogatás a lemezek elsődlegesen meghatározza a felszín nézet a munkadarab, fordult a karakter szükségességét forgácstöréssel vibráció ellenállás és az energiafogyasztás a vágási folyamat. Méretek lemezek, haladva a vágási mélység és a szöget annak érdekében, hogy a szükséges hatásos hossza a vágóél. Attól függően, hogy a feldolgozási erőfeszítés a lemez hossza nagyobb, mint a vágási szélesség 2-4 alkalommal.
Hogy növelje az erejét a vágószerszám, a termelékenység és a minőség kell kiválasztani felületei a lemez egy nagyobb sugarú Apex; A rezgés az elhatárolását a technológiai rendszer.
Csebisev közötti kapcsolat a magassága az érdességi profil R, az R sugár a vertex S és a takarmány a következő formában:
Bár a gyakorlati eredmények eltérhetnek a becsült 2-3 alkalommal, még a köztük nagyolás és feldolgozása van egy szoros korrelációt. Ez különösen igaz a körkörös lemez, amelyre csökkentése érdességi paraméter majdnem arányos az átmérője a lemez.
Mivel anyagok vágórész esztergaszerszámokra használt nagysebességű acélok és cementált karbidok.
1. A sebességű acél R6M5 szokásos teljesítményét, R6MZ, R6M5 és a termelékenység növelése R9K5, R9K10, R10K5F5, R18K5F2 et al. Főleg az alakos vágó, aprító működő nagyolás és fordult, ahol vannak jelentős dinamikus terhelés.
A keménysége Ezen acélok 62. 65 HRC; piros keménysége eléri a 650 ° C-on
Nagy teljesítményű sebességű acél szorosan kapcsolódnak a karbid homogenitás, gondos betartása mód élesítés vágófelületeket, esztergálás nem haladja meg a sebesség 1-1,5 m / s.
2. Kemény ötvözetek találtak a széles körben elterjedt fordult. A fő előnyök a nagy keménységű (82 92 HRA) és gyenge képlékeny alakváltozás (500-700 GPa rugalmassági modulus).
Nagy szakítószilárdság a tömörítési 6 GPa és egy alacsony hőmérsékletű oxidációs előtt lyaemost 873. 1073K lehetővé teszi, hogy növelje a vágási sebesség 2-5-szor, mint a nagy sebességű acél vágóélek.
A hátrányok keményfém elvégzésére van szükség egy viszonylag kis hajlítószilárdság (1,00. 2,5 GPa) és a szívósság.
Karbidok függően változik az összetétele a keményfém szubsztrát.
1) volfrám-karbidot és kobaltot;
2) egy titán-karbid, volfrám és kobalt;
3) a titán-karbidok, volfrám, kobalt és tantál;
4) a karbidok és karbonitridek titán és a kobalt.
Attól függően, hogy milyen típusú feldolgozott anyag és a fordulás karbidok szerint megosztott a nemzetközi szabványok három fő csoportba P, M, R, (lásd a táblázat. 2). Mineralokeramicheskie lemez esztergaszerszámokra gyártják alapján korund (AI2O3).
A magas hőmérsékletű ellenállása akár 1500 ° C-on, mineralokeramicheskie metszőfogak kezelt acél és öntöttvas 5. előformát egy sebesség 10 m / s, de a kis szilárdság (szakítószilárdság hajlítási (1,0-2,5GPa) lehetővé teszi, hogy használja őket csak befejező. a szilárdság növelésére az ásványi kerámia beadott volfrám-karbidok, a titán és a molibdén. Indexelhető sokrétű és körkörös lemez cermetből OT, FOC-60 és a FOC-63 vshuskayut normál és nagy pontosságú befejező. szuperkemény anyagok találtak alkalmazást ve de indexelhető átmérőjű kerek lemezeket 8. 9,5 mm, és a magassága 3-5 mm, gyártja a polikristályos gyémánt vagy köbös bór-nitrid (CBN). Ellenállás a lemezek 5-20-szor magasabb, karbid, amely javítja nemcsak a vágási sebesség, de a és háromdimenziós precíziós forgácsolt alkatrészek.
CBN, amely hőmérséklet-ellenállás szerszám anyagokat 1800 ° C-on, ezekben a polikristályos használt anyagok fordult: Kibora, ismit, Borazon P, P hexán, a kompozit 05, PTNB, belbor.
Mivel inertek sok vas és ötvözetei, CBN lemezek széleskörű alkalmazásra találtak a megmunkálási edzett szén és ötvözött acélok, és újabban - esztergáláshoz speciális ötvözetek és szilárd felrakására.
Polikristályos gyémánt lemez kopásállóság közeledik gyémánt egykristály és ezért a legnehezebb szerszám anyaga. Azonban az alacsony hőmérséklet ellenállás lemezek (650 ° C), és kémiai affinitás a szén lehetővé teszi a legtöbb sikeresen alkalmazzák őket történő elforgatása közben réz, alumínium ötvözetek, különösen nagy szilárdságú műanyagok és kompozit polimer anyagok.
Ezzel párhuzamosan a lemezek szuperkemény anyagok előállított kétrétegű lemez esztergaszerszámokra. Felső szuperkemény polikristályos réteg vastagsága 0,5-1 mm, szintereit kemény fém szubsztrátum nagy statikus nyomáson és hőmérsékleten.
Dupla lap átmérője 10-15 mm, magassága 2-4 mm, elő egy gyémánt-szerű réteget és egy CBN van optimális elastoplastic és kopásállósága a cementált karbid szuperkemény anyagok.
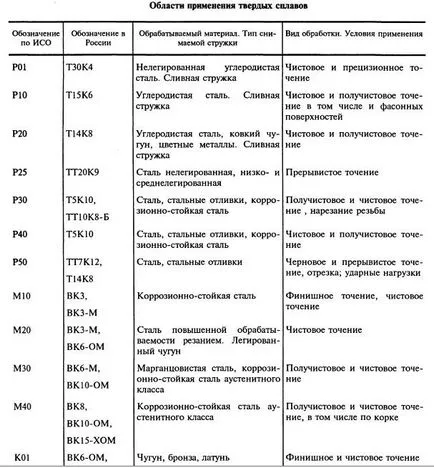
Használata vágó a szuperkemény anyagok feldolgozása során magas edzett ötvözetek 3-5 növeli a fordulópont teljesítményt, mint a keményfém szerszám, miközben növeli a szerszám élettartamát 5-7 alkalommal.
Növeli a termelékenységet a folyamat fordult nagy szilárdságú anyagok elérni, mivel a javulása geometriai paramétereinek forgácsoló részének, változások a fizikai tulajdonságait az anyag esztergált felszíni és a változás a kinematikus rendszerének vágó kölcsönhatás a munkadarab.
Erre a célra használjon vágó rövid elülső felület. a vágóél a párhuzamos és üreges pengék és a fűrészlapot. Változások a fizikai tulajdonságait az anyag a forgácsolási zónában érjük el előre a plasztikus deformáció, a használata különböző fűtési módszerek (plazma, indukciós, lézer, elektromos érintkező, infravörös, elektrolit) vagy hűtés (levegő, emulzió, az emulzió-levegő keverékek).
Megváltoztatása kinetikai vázlata kölcsönhatás érjük körkörös forgó vágó (rotációs vágott) eszközök egy vágóéllel formájában egy spirál (spirális lapátok), és a szuperpozíció rezgés a vágóéi (alacsony frekvenciájú ultrahangos).
Mindezek a módszerek növelik az ellenállást a metszőfogak és a termelékenység növelésére, de a hatékonyság társul számos technológiai és gazdasági korlátok.
Az értékcsökkenés metszőfogak. általában zajlik a hátsó felületen, így a szabványok által elfogadott ez a kritérium megítéléséhez tompa vágó: 0.8. 1,4 mm durva esztergálás, 0,5. 1 mm poluchistovom 0,2. 0,5 mm, ha a befejező. Nagyarányú termelékenység és a minőség megfelelő terméket kapott, amikor fordult a golyó (20 100 m / s), de használata korlátozza a technikai képességek a gépek.
Esztergálásnál viszkózus képződött anyag lefolyó chips okoz csökkentése feldolgozási teljesítmény, különösen automatizált gyártás. Ebben az esetben a forgácstörésre végzik akár a speciális párna a vágólap vagy kinematikai módszerekkel. Vágási adatok fordulópont van rendelve az anyagi és geometriai paramétereit a vágó része a szerszám és a design, a mintegy azaz. Időszakra ellenállás, vágási magasság, takarmány, forgácsolási sebesség, forgácsolási erők és a teljesítmény, valamint az alap időt.
A fejlett technika, az algoritmusok és számítógépes programok lehetővé teszik a számítás, hogy vegye figyelembe az összes korlátok a technológiai rendszer és a részleteket a minőség, valamint hogy végezzen átfogó optimalizálása egyaránt vágás módok és geometriai paraméterei a vágószerszám.
Mivel egyetlen részmunkaidős és a költségek optimalizálása kritériumok elfogadottak, és mindkét figyelembe kell venni együtt, mint azt az időt megfelelő kifejezés értékét.
Optimalizálása fordult 20% növeli a teljesítményt és csökkenti a költségeit a termék, így a leghatékonyabb CNC szerszámgépek és megmunkáló központok.